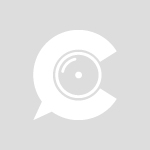
La televisión por protocolo de internet (IPTV) ha revolucionado la forma en que consumimos contenido audiovisual, y uno de los géneros más impactados por esta tecnología es la televisión de realidad (reality TV). Los programas de telerrealidad, que han sido populares durante décadas, están experimentando un renacimiento gracias a las plataformas de IPTV, que ofrecen nuevas posibilidades para la interacción, la personalización y la distribución de contenido listas iptv españa comprar. En este artículo, exploraremos cómo la IPTV está configurando el futuro de la televisión de realidad y qué cambios podemos esperar en los próximos años.
Personalización del contenido en la televisión de realidadUna de las mayores transformaciones que la IPTV trae a la televisión de realidad es la capacidad de personalizar la experiencia del espectador. En la televisión tradicional, los espectadores están limitados a ver lo que los canales deciden emitir en un horario específico. Sin embargo, con IPTV, los usuarios pueden elegir cuándo y qué contenido quieren ver, accediendo a episodios completos bajo demanda. Esto es particularmente relevante para los programas de telerrealidad, que a menudo generan grandes volúmenes de contenido en forma de múltiples episodios, material adicional y escenas detrás de cámaras.
Además, las plataformas de IPTV permiten a los espectadores elegir entre diferentes perspectivas y ángulos de cámara, lo que les otorga una experiencia más inmersiva y personalizada. En programas como Big Brother o Survivor, por ejemplo, los usuarios pueden ver transmisiones en vivo desde diferentes habitaciones o ubicaciones dentro del show, eligiendo a qué participantes quieren seguir más de cerca.
Interactividad: el futuro de la participación del espectadorLa interactividad es otro elemento clave que IPTV está introduciendo en la televisión de realidad. Los espectadores ahora pueden participar de manera directa en los programas, influenciando los resultados a través de votaciones en tiempo real, comentarios o encuestas. Esto no solo aumenta el nivel de compromiso del público, sino que también genera un sentido de participación que va más allá de ser un simple observador.
Un buen ejemplo de este tipo de interactividad son los programas de talentos como La Voz o America's Got Talent, donde los espectadores pueden votar por sus concursantes favoritos en tiempo real utilizando sus dispositivos conectados a internet. En el futuro, podríamos ver un aumento en este tipo de interacción, permitiendo que los espectadores influyan en las decisiones clave del show, como elegir qué desafíos enfrentarán los participantes o qué giros narrativos tomarán las historias.
Acceso global a contenido de telerrealidadOtra ventaja significativa que la IPTV ofrece a la televisión de realidad es el acceso global a una mayor variedad de programas. Antes de la era de la IPTV, los espectadores estaban limitados a los programas que se emitían en su región o país. Ahora, los fanáticos de la telerrealidad pueden acceder a contenido de todo el mundo, descubriendo nuevas culturas y formatos de programas.
Por ejemplo, los usuarios de IPTV pueden ver versiones internacionales de reality shows populares, como MasterChef o Top Model, explorando cómo se adaptan estos formatos a diferentes países y audiencias. Esta globalización del contenido no solo enriquece la experiencia del espectador, sino que también brinda a los productores de telerrealidad la oportunidad de expandir su audiencia y adaptar sus programas para mercados globales.
El futuro de la realidad virtual y aumentada en la telerrealidadUno de los desarrollos más emocionantes que la IPTV está facilitando es la integración de tecnologías emergentes como la realidad virtual (VR) y la realidad aumentada (AR) en la televisión de realidad. A medida que la IPTV sigue evolucionando, los programas de telerrealidad podrían volverse más inmersivos, permitiendo a los espectadores no solo ver, sino también participar en los entornos del programa.
Imagina un futuro en el que los espectadores puedan utilizar dispositivos de VR para entrar virtualmente en la casa de Gran Hermano o para caminar por las playas desiertas de Survivor. Esta inmersión total cambiaría la forma en que experimentamos la televisión de realidad, permitiendo a los fanáticos estar "dentro" del programa, viendo los desafíos y dramas desde una perspectiva mucho más cercana.
ConclusiónLa IPTV está impulsando el futuro de la televisión de realidad hacia nuevas direcciones emocionantes estvservice.com. Con la capacidad de personalizar el contenido, interactuar
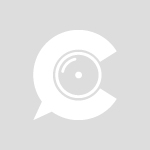
El uso de IPTV (Televisión por Protocolo de Internet) ha demostrado ser una herramienta poderosa en muchos sectores, y el inmobiliario no es una excepción. Con la creciente necesidad de mostrar propiedades de manera eficiente y atractiva, el IPTV se ha posicionado como una tecnología clave para realizar tours virtuales y exhibiciones de propiedades, permitiendo a los compradores potenciales explorar inmuebles desde la comodidad de sus hogares https://www.eiptvservice.com/.
La industria inmobiliaria siempre ha dependido de la capacidad de mostrar propiedades de manera convincente para atraer a posibles compradores. Las visitas físicas a las propiedades siguen siendo importantes, pero no siempre son prácticas, especialmente en el caso de inmuebles ubicados en zonas alejadas o en mercados internacionales. Aquí es donde el IPTV puede marcar la diferencia, ofreciendo tours virtuales en alta definición que permiten a los interesados explorar cada rincón de una propiedad sin tener que estar físicamente presentes.
A través de IPTV, los agentes inmobiliarios pueden transmitir videos en directo o pregrabados de las propiedades, con detalles interactivos que permiten a los espectadores obtener más información sobre características específicas, como dimensiones de las habitaciones, acabados de alta gama o datos sobre el vecindario. La capacidad de transmitir estos tours en cualquier dispositivo conectado a Internet permite que los compradores potenciales tengan acceso a la información sin restricciones de tiempo o ubicación.
Además, el IPTV ofrece la posibilidad de realizar recorridos en tiempo real con interacción directa. Esto significa que los agentes pueden realizar una transmisión en vivo desde una propiedad mientras responden preguntas de los posibles compradores en el momento. Esta función de interacción en tiempo real es especialmente útil para clientes internacionales o aquellos que tienen agendas apretadas y no pueden realizar visitas físicas. También crea un entorno de confianza, ya que los compradores pueden solicitar ver detalles específicos de la propiedad y obtener respuestas inmediatas.
Otra ventaja del IPTV en el sector inmobiliario es la personalización. Las plataformas de IPTV permiten a las agencias inmobiliarias crear canales dedicados para diferentes tipos de propiedades, como residencias de lujo, casas familiares o apartamentos urbanos. Estos canales pueden estar disponibles para un público específico, permitiendo a las agencias segmentar su contenido según el interés de sus clientes. Esta estrategia no solo mejora la visibilidad de las propiedades, sino que también optimiza la experiencia del cliente, quien puede navegar por las propiedades de manera más eficiente.
La integración de tecnologías de realidad aumentada (AR) y realidad virtual (VR) en plataformas de IPTV es otro avance significativo. Con estas herramientas, los clientes no solo pueden ver un video del inmueble, sino que pueden interactuar con un entorno virtual en 3D, donde pueden "caminar" por la propiedad, cambiar ángulos de visión y ver el espacio desde diferentes perspectivas. Esto añade un nivel de inmersión y detalle que supera con creces a las imágenes estáticas o videos tradicionales.
En resumen, el IPTV ha cambiado la manera en que el sector inmobiliario presenta las propiedades. Al ofrecer tours virtuales y exhibiciones de inmuebles a través de plataformas accesibles y de alta calidad, los agentes inmobiliarios pueden captar la atención de compradores potenciales de manera más efectiva, sin las limitaciones de las visitas físicas. Esta tecnología no solo optimiza el proceso de compra, sino que también mejora la experiencia del cliente, creando una conexión más directa y eficiente entre comprador y vendedor.
https://steadyhq.com/en/b67b8a14-56b4-4158-897a-3f0040cc1610/posts/eddf2098-3704-4d4d-9979-12d3c420fc28https://codimd.infn.it/s/FF5-aKC-8https://anotepad.com/notes/nq4cqfrn
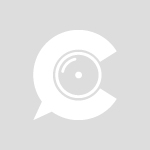
Renting a luxury car doesn’t have to be an extravagant affair reserved for the rich and famous. With a bit of planning, research, and strategic decisions, you can experience the thrill of driving a high-end vehicle without breaking the bank. Here’s how you can rent a car on a budget.
1. Book in AdvanceOne of the simplest ways to save money when renting a luxury car is to book well in advance. Like airline tickets, rental prices often increase as the date approaches, especially for high-demand vehicles like luxury cars. By reserving your car early, you can lock in a lower rate. Rental companies often have promotions or early-bird discounts, which can reduce the cost significantly. Additionally, by planning ahead, you’ll have a better chance of securing the specific model you desire, avoiding any last-minute compromises.
2. Use Price Comparison ToolsSeveral online platforms allow you to compare rental prices across different companies. Websites like Kayak, Expedia, and Rentalcars.com can show you a range of options from various providers, helping you find the best deal on a luxury car. Some of these platforms also offer exclusive discounts or deals if you book through them. Don’t just settle for the first option you find—shop around and take advantage of these tools to find the lowest possible price.
3. Be Flexible with Your Dates and LocationPrices for luxury car rentals can vary significantly depending on the time of the week or season. For instance, renting on a weekday is often cheaper than on weekends, and prices may spike during peak travel periods such as holidays. Flexibility with your rental dates can lead to substantial savings. Similarly, rental rates in major cities are often higher than in smaller towns or suburban locations. If you’re willing to pick up your car from a location outside the city or away from the airport, you might find lower rates.
4. Look for Discounts and Loyalty ProgramsMany rental companies offer discounts for members of specific organizations, such as AAA or AARP. Additionally, some credit cards provide special offers or rewards for car rentals, including luxury vehicles. If you frequently rent cars, consider signing up for a rental company's loyalty program. These programs often provide members with discounted rates, free upgrades, or additional perks. Even if it’s your first rental, some companies will offer a percentage off or a free upgrade for signing up.
5. Consider Short-Term Rentals or Hourly ServicesIf you only need the luxury car for a few hours or a day, consider services like Turo, a car-sharing platform that allows individuals to rent out their vehicles, often at much lower rates than traditional rental companies. Services like Zipcar also offer hourly or daily rentals, which can be more cost-effective if you don’t need the vehicle for an extended period. You can still enjoy the luxury experience without paying for days you won’t use.
6. Avoid Extra ChargesWhen renting a luxury car, it’s important to be aware of the potential extra charges that can quickly add up. For example, insurance packages offered by rental companies are often more expensive than necessary, especially if your personal car insurance or credit card already covers rentals. Be sure to check what coverage you already have before agreeing to additional charges. Also, refuel the car yourself before returning it, as rental companies typically charge a premium for refueling services.
7. Negotiate and Look for Last-Minute DealsIt may sound surprising, but you can sometimes negotiate a better rate directly with the rental company, especially if the car hasn’t been booked by anyone else close to your rental date. Some agencies would rather rent the car at a discounted rate than leave it sitting idle. Also, look for last-minute deals; occasionally, companies will offer significant discounts to fill vacant cars.
In conclusion, renting a luxury car from https://www.voyagecopilot.com/car/ng/provider-at-station/3172/autovia-car-hire-bologna-central-station on a budget is achievable if you’re willing to put in a little extra effort. By booking early, comparing prices, taking advantage of discounts, and avoiding unnecessary charges, you can drive the car of your dreams without straining your finances. Whether it’s for a special occasion or just to experience the thrill, there are plenty of ways to enjoy the luxury car rental experience affordably.